Safety First
OKFACE Report #00-OK-004-01
SUBJECT: Oilfield trainee died after being struck by a bull plug, needle valve and gauge assembly blown out of a wellhead connection
Figure 1. Position of victim in relation to the wellhead and location of bull plug after it flew out of the wellhead and struck the victim.
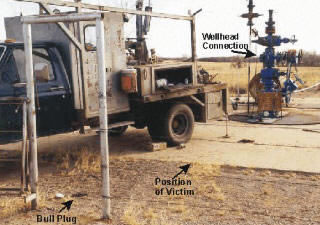
SUMMARY: A 19-year old wireline operator trainee died on January 12, 2000, from head and neck trauma received at an oil well when he was struck by a bull plug, needle valve and pressure gauge assembly that had been blown out of a wellhead connection. At the time of the incident, the victim was standing approximately 15 feet away from the wellhead near the wireline truck where he and the wireline operator were changing wireline tools while the well operator and an oilfield chemical service representative were attempting to gauge the well pressure. When the well operator opened the wellhead gate valve, the bull plug, needle valve and gauge assembly blew out of the connection and struck the victim in the head and neck inflicting fatal injuries. OKFACE investigators concluded that to prevent similar occurrences:
- The responsible employer on multi-employer worksites should monitor critical safety activities performed by contractor employees, particularly personnel whose background and skills may be unknown or uncertain.
- Until connections are adequately tested, the responsible employer on oil well locations should place signs or barricades in areas that lie in direct line with wellhead flanges and connections that may be subject to flying debris in the event of a system failure.
- The responsible employer on multi-employer job sites should plan and coordinate job activities and communicate planned operations and their associated hazards with representatives from each organization working at the site.
- Employers should develop and implement a formal occupational health and safety management system that is focused on continual improvement.
- Employers should ensure that all employees are properly trained and skilled to perform each task that they are assigned, including training in hazard recognition and control.
INTRODUCTION
A 19-year old wireline operator trainee for an oil well wireline service contractor died on January 12, 2000, from head and neck injuries received when he was struck by a bull plug, needle valve and pressure gauge assembly that had been blown out of a wellhead connection. The natural gas well had been in production approximately 20 years and was approximately 18,000 feet deep. OKFACE investigators reviewed OSHA reports, the death certificate, and the medical examiner’s report. While conducting the site survey, OKFACE investigators interviewed the wireline company owner.
Wireline services are one of a variety of contractors that oil well operators may use during the preparation and production of a well. The wireline service company employed five people and had been in business for 16 years without a serious injury. The company had employed the decedent for nine days prior to the day of the incident. On the day of the incident, the trainee and an experienced wireline operator had initiated work at the first of two rural well sites to be serviced by the crew that day. The company had a written safety program that was essentially a compilation of safety requirements established by the various well operators for whom the company normally performed services. All new employees received orientation that covered safety information included in the written program and on-the-job training under the supervision of an experienced operator. The hazard that resulted in the fatality was not specifically addressed in the written safety program, but was addressed informally.
INVESTIGATION
Figure 2. Bull plug, needle valve and gauge assembly
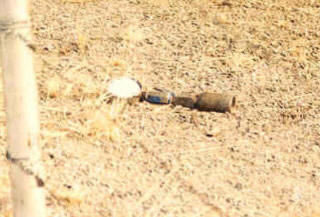
The well operator, a two-person wireline crew, and a chemical company operator were at the well site at the time of the fatal incident. The well operator was onsite to coordinate the activities and operate wellhead equipment. He had contracted the wireline service to obtain information about the well bore and the production tubing within the well bore. The well operator had also retained the services of a chemical company, whose driver/operator was onsite with a tanker truck at the time to make the wellhead connection and pump corrosion-inhibiting chemicals into the well.
Before the incident occurred, the wireline crew had made one run into the well and had pulled back out of the well to change tools. At approximately 10:30 a.m., while the wireline crew was changing tools near their truck, the well operator and the chemical company operator attempted to gauge the well pressure (later estimated to be approximately 1400 psig). The chemical company operator inserted a gauge assembly, consisting of a bull plug, needle valve and pressure gauge, into a threaded flange on the wellhead and tightened the assembly until it was snug. The well operator, who had been in his truck using a mobile phone, came back to the wellhead, noticed that the gauge rigging was in place, and proceeded to open the gate valve to conduct the pressure check. The wireline crew trainee was standing next to his crew truck approximately 15 feet from the wellhead in direct line with the wellhead connection (Figure 1). When the gate valve was opened, the sudden pressure dislodged the bull plug and blew the plug, needle valve and gauge assembly out of the flange in the direction of the wireline operator trainee, striking him in the head and neck (Figure 2). The force of the impact knocked the trainee into the wireline operator who had been standing a few feet away.
Figure 3. Wellhead Connection
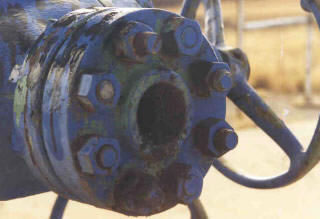
Investigators determined that the chemical company operator had inserted a standard 2- inch pipe bull plug into a 2-3/8 inch eight round external upset threaded flange which may have appeared to accept the connection (Figure 3). However, only the crown of the threads were in contact with each other and none of the threads were actually engaged. The mismatched threads did not hold the assembly in place when the wellhead valve was opened. The well operator did not inspect the gauge assembly before opening the gate valve.
After the incident occurred, the well operator called 911 and an ambulance crew was dispatched from the nearest town, approximately 10 miles from the site of the incident. The victim was transported to the local hospital where he was given life support and trauma care to the extent feasible at the hospital. The victim was later transported by helicopter to a trauma center for more advanced care, but he was pronounced dead approximately eight hours later.
CAUSE OF DEATH
The Medical Examiner listed the cause of death as head and neck trauma.
RECOMMENDATIONS
Recommendation #1: The responsible employer on multi-employer worksites should monitor critical safety activities performed by contractor employees, particularly personnel whose background and skills may be unknown or uncertain.
Discussion: The application of an improper fitting to the wellhead was an underlying cause of the fatal incident. The assumption that the gauge assembly was properly connected proved to be inaccurate, and the action to open the valve and pressurize the gauge assembly became an underlying cause of the fatal incident. The fatality may have been prevented if the gauge assembly was checked to assess its reliability before opening the well valve. Evaluation/assessment of the knowledge and skills of subcontractor operatives and inspection and monitoring of critical operations that they perform is a prudent management practice.
Recommendation #2: Until connections are adequately tested, the responsible employer on oil well locations should place signs or barricades in areas that lie in direct line with wellhead flanges and connections that may be subject to flying debris in the event of a system failure.
Discussion: The physical location of the decedent with respect to the wellhead connection was an underlying cause of the fatal incident. The victim may not have been aware that he was standing in a location subject to a flying projectile when the gauge assembly was blown out of the wellhead connection. Worksites should be laid out with vehicles and adjoining work spaces positioned out of direct line with any connections to be used during the day’s activities and with hazardous areas well marked to prevent persons from inadvertently walking into an area in direct line with any connection in use. Signs or barricades that cordoned off the danger zone may have deterred the victim from being in a position where he could be struck when the gauge assembly was blown out of the well connection.
Recommendation #3: The responsible employer on multi-employer job sites should plan and coordinate job activities and communicate planned operations and their associated hazards with representatives from each organization working at the site.
Discussion: The responsible employer should communicate the nature of the work to be performed and the hazards associated with each aspect of the work (an existing requirement under certain OSHA regulations such as Hazard Communication and Permit-Required Confined Spaces). The responsible employer should ensure that personnel involved in hazardous activities have adequate training and skills for the tasks they are to perform. The responsible employer should also exercise diligence to ensure that contracted personnel are performing their work properly and safely in accordance with the operational plan.
Recommendation #4: Employers should develop and implement a formal occupational health and safety management system that is focused on continual improvement.
Discussion: The dynamic nature of the contemporary workplace necessitates a management model that ensures continual improvement in virtually all aspects of the business. This principle is particularly critical with regard to the management of workplace health and safety, which must be integrated into all operational aspects of an organization’s business plan. While implementation of a system such as the Occupational Health and Safety Assessment Series (OHSAS 18001) may or may not have directly affected outcome of this incident, it could have encouraged and facilitated the identification and correction of deficiencies that served as contributing causes. It would also encourage and facilitate the general improvement of occupational health and safety performance throughout the organization.
Recommendation #5: Employers should ensure that all employees are properly trained and skilled to perform each task that they are assigned, including training in hazard recognition and control.
Discussion: The insertion of mismatched threads on the bull plug, needle valve and gauge assembly into the wellhead flange was an underlying cause of the fatal incident. The improper connection was reportedly identifiable by visual or physical inspection by an experienced worker. The improperly threaded connection evidences a lack of understanding regarding the equipment, the task, or the hazards presented by the use of the wrong fitting in the wellhead connection. The knowledge and skills of all workers should be assessed and adequate training provided by the employer before assigning them to perform critical tasks. Additionally, training in hazard recognition and control should be provided to all workers who work in proximity of wells. Training should address the potential for blowouts and should provide clear directions to remain outside the area directly in front of the wellhead connection.
REFERENCES
- 29 CFR 1910.145, Specifications for accident prevention signs and tags.
- American Petroleum Institute, Occupational Safety for Oil and Gas Well Drilling and Servicing Operations (API RP54).
The Oklahoma Fatality Assessment and Control Evaluation (OKFACE) is an occupational fatality surveillance project to determine the epidemiology of all fatal work-related injuries and identify and recommend prevention strategies. FACE is a research program of the National Institute for Occupational Safety and Health (NIOSH), Division of Safety Research.
These fatality investigations serve to prevent fatal work-related injuries in the future by studying the work environment, the worker, the task the worker was performing, the tools the worker was using, the energy exchange resulting in injury, and the role of management in controlling how these factors interact.